Heat exchangers are crucial components in a wide range of industries, including automotive, power generation, HVAC, and even electronics. Traditionally made from metal, heat exchangers are used to transfer heat between two or more fluids (liquid or gas) without the fluids mixing. However, in recent years, ceramic heat exchangers have gained popularity due to their exceptional heat resistance, durability, and ability to withstand harsh environments. This article will explore how ceramic heat exchangers work, their advantages, applications, and why they are becoming increasingly important in advanced technologies.
What Is a Ceramic Heat Exchanger?
A ceramic heat exchanger operates similarly to a traditional metal heat exchanger. Its primary function is to transfer heat between two different media (gases, liquids, or a combination) without the fluids mixing. The key difference is the material—ceramic heat exchangers use advanced ceramic materials instead of metals.
Why Use Ceramic?
Ceramic materials are known for their high-temperature resistance, corrosion resistance, and thermal stability. Unlike metals, which can degrade or lose efficiency at extreme temperatures, ceramics can maintain their integrity, making them ideal for high-temperature and high-corrosion environments.
How Do Ceramic Heat Exchangers Differ from Metal Ones?
- Temperature Resistance: Ceramics can withstand temperatures above 1000°C (1832°F), while metals like steel or aluminum degrade at lower temperatures.
- Corrosion Resistance: Ceramics are resistant to chemical reactions, making them ideal in industries where the media could be corrosive.
- Thermal Shock Resistance: Ceramics have the ability to resist sudden changes in temperature, reducing the risk of cracking.
- Longevity: Due to their resistance to wear and tear, ceramic heat exchangers often last longer than metal ones in demanding environments.
Structure of Ceramic Heat Exchangers
Ceramic heat exchangers are typically designed in a similar fashion to metal heat exchangers, with tubes, plates, or finned designs. The structure allows for efficient heat transfer, but ceramics bring additional benefits, such as lighter weight and less risk of deformation under thermal stress.
How Do Ceramic Heat Exchangers Work?
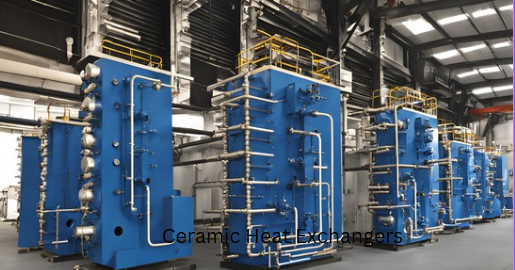
Principle of Operation
The operation of a ceramic heat exchanger follows the same basic principle as any heat exchanger: it allows for the transfer of heat between two or more fluids while keeping them separate. Here’s a breakdown of the process:
- Heat Transfer: One fluid, which could be air, water, or another gas or liquid, flows through a series of ceramic tubes or plates. As it moves through the system, it heats the ceramic material.
- Heat Retention: Due to ceramics’ excellent thermal conductivity and heat retention, the heat is absorbed by the ceramic components and transferred to the adjacent fluid flowing on the other side of the tubes or plates. This process ensures efficient heat transfer while preventing the two fluids from mixing.
- Thermal Efficiency: Ceramic heat exchangers can maintain higher thermal efficiency even in harsh environments due to the superior properties of ceramics. This is particularly useful in processes where high-temperature gases or chemicals are involved.
Applications of Ceramic Heat Exchangers
Ceramic heat exchangers are ideal for industries that deal with high-temperature processes and corrosive gases. Some common applications include:
Waste Heat Recovery: In industries like steel production or power generation, high-temperature waste gases can be passed through a ceramic heat exchanger to recover energy, which can then be reused, improving overall efficiency.
Chemical Processing: Many chemical reactions take place at high temperatures and involve corrosive substances. Ceramic heat exchangers are ideal for transferring heat in these environments because they resist both heat and corrosion.
Automotive Industry:
In vehicles, ceramic heat exchangers are used in exhaust gas recirculation (EGR) systems to reduce emissions. The high-temperature exhaust gases are cooled down before being recirculated into the engine.
HVAC Systems: Ceramic heat exchangers are used in high-efficiency furnaces and heating systems, where durability and resistance to corrosion are key for long-term performance.
Fuel Cells: Ceramic materials are often used in solid oxide fuel cells (SOFCs) to facilitate the efficient transfer of heat at high temperatures.
Solar Power Plants: In solar thermal power plants, ceramic heat exchangers help in transferring heat from concentrated sunlight to fluids that generate electricity.
Benefits of Ceramic Heat Exchangers
1. High-Temperature Performance
Ceramics can withstand extremely high temperatures without degrading, making them ideal for processes that require continuous heat exposure.
2. Durability
Ceramic materials are more durable than metals in harsh environments. They are resistant to both physical and chemical wear, which means fewer replacements and lower maintenance costs over time.
3. Lightweight
Ceramic materials are often lighter than their metal counterparts, which can reduce the overall weight of the system, particularly in mobile applications like automobiles or aerospace.
4. Corrosion Resistance
Unlike metals, which can corrode when exposed to acidic or corrosive environments, ceramics remain stable, which is critical in industries like chemical processing or waste management.
5. Energy Efficiency
Due to the superior thermal conductivity and heat retention properties of ceramics, heat exchangers made from this material can transfer heat more efficiently, reducing energy consumption.
6. Environmental Benefits
By using ceramic heat exchangers in waste heat recovery systems, industries can reduce their environmental footprint by recovering and reusing energy that would otherwise be wasted.
Challenges of Ceramic Heat Exchangers
While ceramic heat exchangers offer many benefits, there are also challenges:
- Cost: Ceramic materials are generally more expensive than metals, which can make the initial investment higher.
- Fragility: Although ceramics are durable, they can be brittle and prone to cracking under mechanical stress.
- Manufacturing Complexity: Producing ceramic heat exchangers can be more complex due to the advanced materials and processes required.
Maintenance of Ceramic Heat Exchangers
One of the key advantages of ceramic heat exchangers is their low maintenance needs. However, to ensure longevity and efficiency, here are a few best practices:
- Regular Cleaning: Over time, deposits or build-up from the fluids being processed can accumulate on the ceramic surfaces. Regular cleaning can help maintain efficient heat transfer.
- Inspection for Cracks: Although ceramic is resistant to thermal shock, it can still develop cracks under certain conditions. Routine inspections can catch any early signs of damage.
- Protect Against Abrasive Media: In systems where abrasive materials are involved, it’s important to monitor wear and tear on the ceramic surfaces to prevent erosion.
FAQs
1. What are ceramic heat exchangers used for?
Ceramic heat exchangers are used in industries where high temperatures and corrosive environments are present, such as chemical processing, automotive systems, and waste heat recovery.
2. How do ceramic heat exchangers differ from metal ones?
Ceramic heat exchangers can withstand higher temperatures and resist corrosion better than metal heat exchangers. They also have a longer lifespan in harsh conditions.
3. Are ceramic heat exchangers expensive?
Yes, ceramic heat exchangers are typically more expensive than their metal counterparts due to the cost of the materials and the complexity of the manufacturing process.
4. Can ceramic heat exchangers break?
Ceramics can be brittle and prone to cracking under mechanical stress, so while they are highly durable in terms of heat and corrosion resistance, care must be taken to avoid physical impacts.
5. What industries benefit from ceramic heat exchangers?
Industries such as power generation, chemical processing, automotive, HVAC, and solar power benefit from the durability, heat resistance, and efficiency of ceramic heat exchangers.
6. Do ceramic heat exchangers improve energy efficiency?
Yes, ceramic heat exchangers can improve energy efficiency due to their superior heat retention and thermal conductivity properties, which enable better heat transfer and waste heat recovery.
7. Can ceramic heat exchangers be used in fuel cells?
Yes, ceramic materials are used in solid oxide fuel cells (SOFCs) due to their ability to handle high temperatures and facilitate efficient heat transfer.
8. What is the lifespan of a ceramic heat exchanger?
The lifespan of a ceramic heat exchanger can be significantly longer than that of a metal one, especially in high-temperature and corrosive environments, provided it is properly maintained.
9. Can ceramic heat exchangers be used in HVAC systems?
Yes, ceramic heat exchangers are increasingly used in high-efficiency HVAC systems, particularly in systems that require long-term durability and resistance to corrosion.
10. Are ceramic heat exchangers environmentally friendly?
Yes, ceramic heat exchangers contribute to environmental sustainability by improving energy efficiency and enabling waste heat recovery, which reduces the overall energy consumption of industrial processes.
Conclusion
Ceramic heat exchangers represent a significant advancement in heat transfer technology, particularly in industries where high temperatures, harsh chemicals, and corrosive environments are present. With their superior thermal properties, durability, and resistance to corrosion, ceramic heat exchangers are ideal for applications ranging from waste heat recovery to automotive exhaust systems and beyond.
While they may come at a higher initial cost, their longevity, efficiency, and reduced maintenance requirements make them a wise investment for industries seeking long-term energy savings and environmental benefits. Whether in the chemical, automotive, or renewable energy sectors, ceramic heat exchangers are increasingly becoming a critical component in modern industrial processes.