Ceramic glazes are an essential component of pottery and ceramic art, transforming raw clay into beautiful, functional, and durable pieces. If you’ve ever wondered, “What is a ceramic glaze?” you’re not alone. This article will delve into the world of ceramic glazes, exploring their composition, types, application techniques, and the role they play in creating stunning ceramic pieces. Whether you’re a beginner or an experienced ceramic artist, this guide will provide valuable insights into the art and science of ceramic glazing.
What is a Ceramic Glaze?
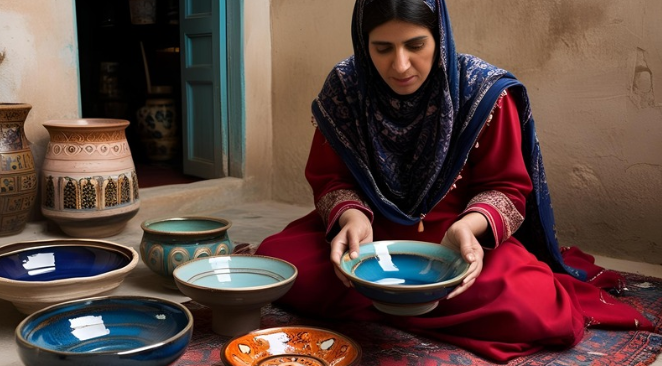
View Glazed Ceramics on Amazon
A ceramic glaze is a glass-like coating applied to ceramic pieces to enhance their appearance, durability, and functionality. Glazes are made from a mixture of minerals, oxides, and other materials that, when fired at high temperatures, melt and fuse to the surface of the ceramic piece. The result is a smooth, glossy, or matte finish that can be decorative, protective, or both.
Ceramic glazes serve several purposes:
- Aesthetic Enhancement: Glazes add color, texture, and visual appeal to ceramic pieces.
- Functional Protection: Glazes make ceramic surfaces waterproof, stain-resistant, and easier to clean.
- Durability: Glazes strengthen ceramic pieces, making them more resistant to wear and tear.
The Composition of Ceramic Glazes
Ceramic glazes are composed of three main components: fluxes, stabilizers, and glass formers. Each component plays a critical role in the glaze’s performance and appearance.
1. Fluxes
Fluxes are materials that lower the melting point of the glaze, allowing it to fuse to the ceramic surface at lower temperatures. Common fluxes include:
- Sodium oxide (Na₂O)
- Potassium oxide (K₂O)
- Calcium oxide (CaO)
2. Stabilizers
Stabilizers help control the glaze’s melting behavior and prevent it from running off the ceramic piece during firing. Common stabilizers include:
- Alumina (Al₂O₃)
- Silica (SiO₂)
3. Glass Formers
Glass formers are the primary components that create the glassy surface of the glaze. The most common glass former is silica (SiO₂), which melts and forms a glassy layer when fired.
In addition to these primary components, ceramic glazes may contain colorants (such as metal oxides) and additives (such as opacifiers or texturizers) to achieve specific effects.
Types of Ceramic Glazes
Ceramic glazes come in a wide variety of types, each with its unique properties and applications. Here are some of the most common types of ceramic glazes:
1. Transparent Glazes
Transparent glazes are clear and allow the underlying clay body or decoration to show through. They are often used to enhance the natural beauty of the clay or to protect painted or carved designs.
2. Opaque Glazes
Opaque glazes are non-transparent and completely cover the clay body. They are ideal for creating solid, uniform colors and hiding imperfections in the clay.
3. Matte Glazes
Matte glazes have a non-reflective, smooth finish. They are popular for creating a soft, understated look and are often used in contemporary ceramic art.
4. Gloss Glazes
Gloss glazes have a shiny, reflective finish. They are commonly used for functional ware, such as dishes and mugs, as they create a smooth, easy-to-clean surface.
5. Textured Glazes
Textured glazes create a tactile surface with variations in thickness, pattern, or relief. They are often used for decorative pieces to add visual and tactile interest.
6. Crystalline Glazes
Crystalline glazes are specialized glazes that form crystal patterns during the firing process. They require precise temperature control and are often used for artistic and decorative pieces.
7. Raku Glazes
Raku glazes are designed for the raku firing process, which involves removing the ceramic piece from the kiln at high temperatures and placing it in a reduction environment. This creates unique, unpredictable effects, such as metallic finishes and crackled surfaces.
8. Underglazes
Underglazes are applied to the clay surface before the glaze and are often used for detailed designs or patterns. They remain visible after the glaze is applied and fired.
9. Overglazes
Overglazes are applied on top of a fired glaze and are often used for additional decoration, such as luster or enamel finishes.
10. Food-Safe Glazes
Food-safe glazes are specifically formulated to be non-toxic and safe for use on functional ware, such as plates, bowls, and mugs. They must meet strict safety standards to ensure they do not leach harmful substances into food or drink.
How is Ceramic Glaze Applied?
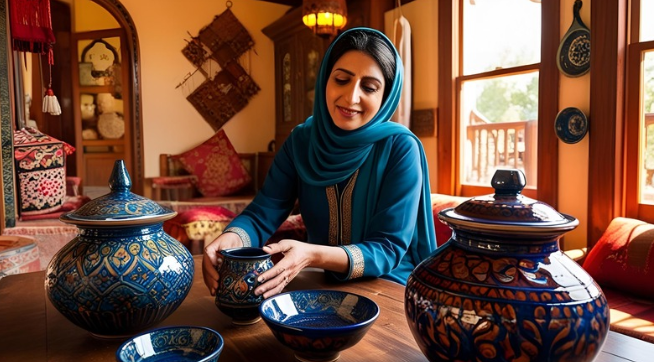
The application of ceramic glaze is a critical step in the ceramic-making process. There are several methods for applying glaze, each with its unique advantages and effects:
1. Brushing
Brushing is one of the most common methods of applying glaze. It involves using a brush to apply the glaze evenly to the ceramic surface. This method is ideal for detailed work and small pieces.
2. Dipping
Dipping involves submerging the ceramic piece into a container of glaze. This method ensures even coverage and is often used for larger pieces or when a uniform finish is desired.
3. Pouring
Pouring involves pouring glaze over the ceramic piece. This method is often used for creating layered or textured effects.
4. Spraying
Spraying involves using a spray gun or airbrush to apply the glaze. This method is ideal for achieving smooth, even coverage on large or complex pieces.
5. Sponging
Sponging involves using a sponge to apply the glaze. This method is often used for creating textured or mottled effects.
6. Wax Resist
Wax resist involves applying wax to certain areas of the ceramic piece before glazing. The wax prevents the glaze from adhering to those areas, creating patterns or designs.
The Firing Process
Once the glaze is applied, the ceramic piece must be fired in a kiln to achieve its final form. The firing process involves heating the piece to high temperatures, typically between 1,800°F and 2,400°F, depending on the type of glaze and clay used. During firing, the glaze melts and fuses to the ceramic surface, creating a durable, glass-like coating.
Key Stages of Firing:
- Bisque Firing: The first firing, which hardens the clay and prepares it for glazing.
- Glaze Firing: The second firing, which melts the glaze and bonds it to the ceramic surface.
FAQs: What is a Ceramic Glaze?
1. What is a ceramic glaze made of?
A ceramic glaze is made of fluxes, stabilizers, and glass formers, along with colorants and additives to achieve specific effects.
2. What is the purpose of a ceramic glaze?
Ceramic glazes enhance the appearance, durability, and functionality of ceramic pieces by adding color, texture, and a protective coating.
3. Are ceramic glazes safe for food use?
Food-safe glazes are specifically formulated to be non-toxic and safe for use on functional ware. Always check the label to ensure the glaze is food-safe.
4. Can I mix different glazes?
Yes, glazes can be mixed to create custom colors and effects. However, it’s important to test the mixture before applying it to your final piece.
5. How do I apply ceramic glaze?
Ceramic glaze can be applied by brushing, dipping, pouring, spraying, sponging, or using wax resist techniques.
6. What is the difference between underglaze and overglaze?
Underglaze is applied before the glaze and remains visible after firing, while overglaze is applied on top of a fired glaze for additional decoration.
7. What is a crystalline glaze?
Crystalline glazes form crystal patterns during the firing process and require precise temperature control.
8. Can I glaze pottery at home?
Yes, you can glaze pottery at home using a kiln. However, proper ventilation and safety precautions are essential.
9. How do I fix a cracked glaze?
A cracked glaze can sometimes be repaired by reapplying glaze and refiring the piece. However, prevention is key—ensure even application and proper firing temperatures.
10. What is raku glaze?
Raku glaze is designed for the raku firing process, which creates unique, unpredictable effects like metallic finishes and crackled surfaces.
Conclusion: What is a Ceramic Glaze?
Ceramic glazes are a fascinating and essential aspect of pottery and ceramic art. They transform raw clay into beautiful, functional, and durable pieces by adding color, texture, and protection. Understanding the composition, types, and application techniques of ceramic glazes can help you create stunning ceramic pieces that reflect your artistic vision.
Whether you’re a beginner or an experienced ceramic artist, experimenting with different glazes and techniques can open up a world of creative possibilities. From transparent and opaque glazes to textured and crystalline finishes, the options are endless. So, the next time you ask, “What is a ceramic glaze?” remember that it’s not just a coating—it’s a gateway to artistic expression and functional beauty.